OALP XIX Seminar 5
Wednesday, Jan. 16, 2019
Wednesday morning, the group loaded the bus in Stillwater to head to our first stop of the seminar: HANOR Family of Companies headquarters in Enid. Jeff Mencke, director of Oklahoma operations at HANOR, greeted us and explained the operations of HANOR. HANOR has packing plants in Missouri and a large amount of their pork goes to export. They are an exporter of premium pork products worldwide. The HANOR Company owns 17,900 acres with farms in Illinois (North Carolina and Oklahoma for sows), Iowa, South Dakoto, Wisconsin, Ohio, Montana, Utah and Missouri. Most pigs are finished in Iowa. They have 780 animal barns nationwide and the majority are in Iowa because of the finishing sites.
HANOR has an extensive research program. R&D works to integrate science into practical application with focus on ROI and benefit to the consumer. They have a farm in Mooreland, Oklahoma, where they do most of their sow research field validation and financial assessment in the research loop. They also research fertility and nutrition.
They have a strong veterinary program and health assurance program. They have three veterinarians in Iowa and five full-time DMVs on staff. They have custom autogenous vaccine production and try to develop their own vaccination program. Autogenous inoculum production: they have a diagnostic and molecular biology lab in Iowa and can develop inoculum. They have extensive biosecurity and protect their animals from people or any kind of vector. They have companywide restricted access to farms. The truck wash has several washing bays and two baking bays. A trailer that goes to the farm location is heated to 180 degrees before it goes out to the farm. Porcine epidemic diarrhea has really upped the game for biosecurity.
For their feed milling operation, they utilize 22.5 million bushels of U.S. corn each year from 130,000 acres. A total of 920,000 tons of complete feed is delivered annually from 18 feed manufacturing plants which is 3,500 tons of complete feed each day on 46 semi loads covering 8,200 miles and using 1,800 gallons of fuel. HANOR recycles 32 semi loads per day of byproducts from human food and ethanol industries.
HANOR was recognized in 2012 as a National Pork Industry Environmental Steward Award winner and won the state and national environmental stewardship award. Compared to 50 years ago, pork producers are using less land and water to produce pork. And they are doing it with a smaller carbon footprint – 78% less land, 41% less water, and 35% smaller carbon footprint.
HANOR’s business fundamentals are of long-term viability. Efficiency is key. Their vision is focused on an unwavering belief in that vision, do things the right way, and be prepared to move at the right time.
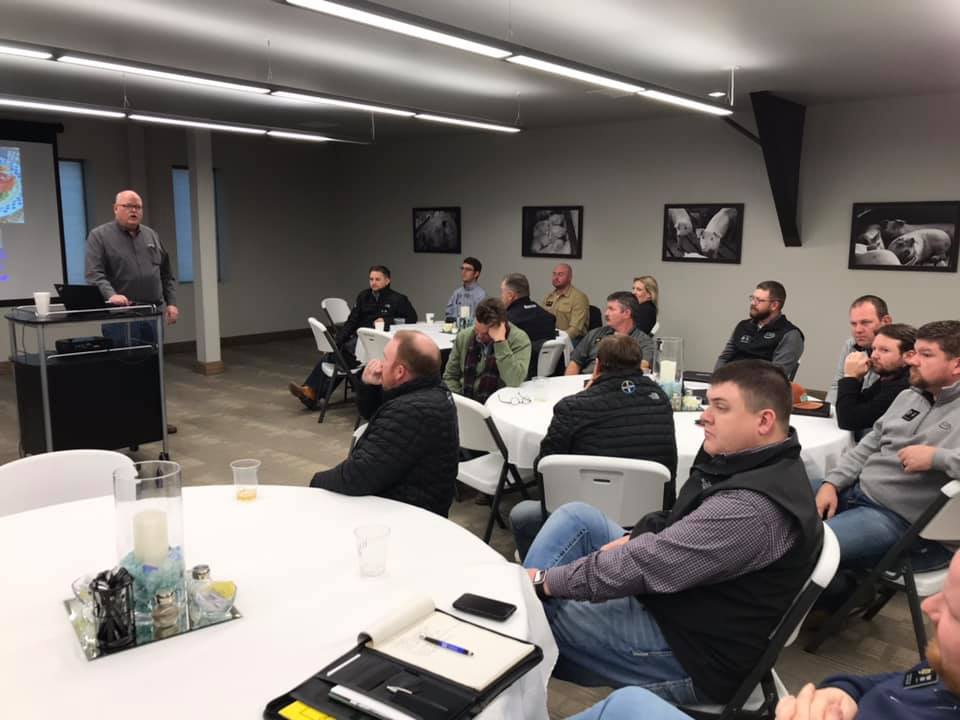
The next stop of the day was Johnston Seed Company. Joey Meibergen, a member of Class XIII and President/CEO of Johnston Seed Company, and John Lamle gave us an overview of the company. Johnston Seed Company was founded on the hills of the Cherokee Strip land run. W.B. Johnston had his wife participate in the land run and she shot a man who tried to steal her land. After the land run, everyone needed to buy supplies, so W.B. saw an opportunity. He bought the local feed and seed store and then bought winter wheat from Kansas. He would loan seeds to plant the first season and farmers would pay him back two times what they grew and that’s how it started 125 years ago.
They have their own breeding program and have warm-season species. They also license the technologies they have developed. They have created partnerships with some businesses and license the technology and give them an exclusive market to sell that variety. They are currently working on two plant patents for new vegetative bermudagrasses. The environmental conservation seeds work with a lot of native grasses and species that go into the habitats for pollinators and help out the Oklahoma conservation program.
They clean and process all of their seeds. They have 400-450 SKUs. If you include all small grains and all varieties of grass crops, etc., they have around 1000 SKUs. There is no crops insurance for what they grow.
Their breeding program is all traditional breeding. Wrangler bermudagrass is cold tolerant and the most widely planted variety (southern 2/3 of what’s sold in the U.S.). Riviera is a standard in the bermudagrass industry and really helped put them on the map like Wrangler. Wind farms are in native grass areas and they provide grass for them. Wildflower programs are dependent on government programs and they grow over 600 acres of wildflowers. The natural bees or pollinators aren’t out as much as they were before.
After picking up seeds with a combine, they sift for trash and clean to get pure materials. They aerate these seeds with ambient air and then they turn it and grind the seed to knock off excess material and make the particle size a little smaller. They have different sieves for each process.
Our planned visit to Bennie’s Barn Equine Therapy and Riding Facility for our community service project of painting the outdoor arena was canceled due to rain. Therefore, we made a brief stop at the Vietnam Memorial Wall at the Woodring Regional Airport in Enid.
We ended the day with a delicious chili dinner provided by Don Schieber and his family at his farm. We enjoyed a nice warm meal on a chilly day along with some great conversations. Afterwards, we headed to the hotel in Wichita, KS.
Thursday, Jan. 17, 2019
Day two started at Cargill visiting with members of the Cargill Protein division, also known as Cargill Meat Solutions. They are headquartered in Wichita, Kansas, and just unveiled a new building in October that houses 800 employees in a modern workspace.
Dr. Glen Dolezal shared that Cargill Protein focuses on the center of the plate with their core products being beef, turkey and eggs. Our conversation with Cargill Protein focused on beef production and the different grades of Prime, Choice, Select and No Roll, and how those grades are assigned. Cargill uses a combination of dentition to determine the age of the animal and camera grading. These methods bring tremendous efficiency and consistency to their operations and bottom line.
Animal welfare and safety are on top of the minds of all employees of Cargill. Cameras are placed throughout the plant. Every step of the process is tracked and reviewed, and third party auditing takes place to ensure the animals are being handled humanely. Robots are used in the cattle pens to move cattle around rather than having a person in a dangerous situation in tight quarters.
We heard from Beef Economist Brian Highfill and learned how weather patterns, grain markets and consumer demand all play a role in the beef supply. In 2018, there was a record level of beef production and 2019 production is expected to grow 2% or more. Imports are steady from one year ago with most coming from Australia. Exports finished at a record level for 2018, about 10% above 2017, and 2019 is expected to be slightly more moderate. Per capita beef consumption dropped nearly 17 pounds from 2006 with most of that going to broilers. Consumer confidence is at an all-time high.
Cargill is looking around the industry and agriculture, trying to ensure they stay ahead of issues and challenges coming their way. Mike Martin talked about the U.S. government shutdown, trades disputes, labor and immigration, food safety and animal welfare. He focused on how these in combination are a challenge for Cargill and their customers throughout the supply chain. They are looking at each one individually and to make sure they are approaching them correctly.
Sustainability also is a major topic of discussion and action for Cargill. Meghan Mueseler discussed what sustainability means to Cargill and how that links with their mission of feeding 9 billion people by 2050. They are employing a three-prong approach to sustainability – social, environmental and economic. Their corporate priorities are on climate change, land use, water resources, farmer livelihoods and food waste. They are utilizing video series, websites and the Midwest Row Crop Collaborative to tell their story. They are also involved in the U.S. Roundtable for Sustainable Beef which has a vision of the U.S. beef value chain being the trusted global leader in environmentally sound, socially responsible and economically viable beef.
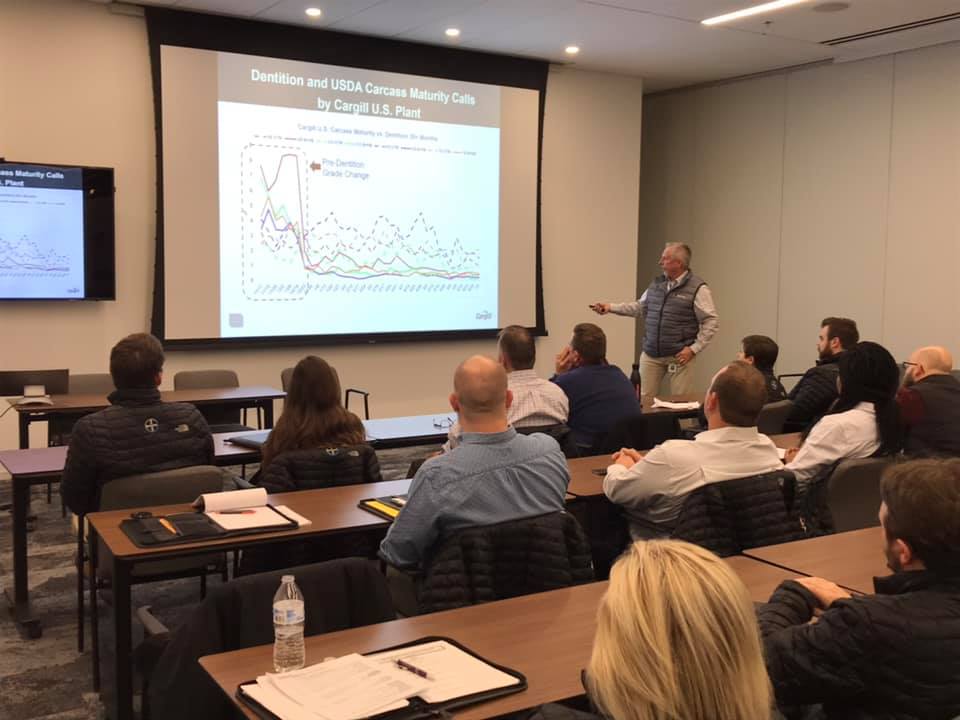
We then traveled across town to visit Ardent Mills. They are a Joint Venture company between Con Agra and Horizon Milling (CHS and Cargill). They are the largest miller in the U.S. with 42 processing facilities and 2,500 employees processing almost all types of grains. There are 75 people employed at the Wichita mill and they turn 65,000 bushel of hard red winter wheat into 3 million pounds of finished flour per day. One loaf of bread uses about one pound of flour and so does a pizza…that’s a lot of pizza and bread.
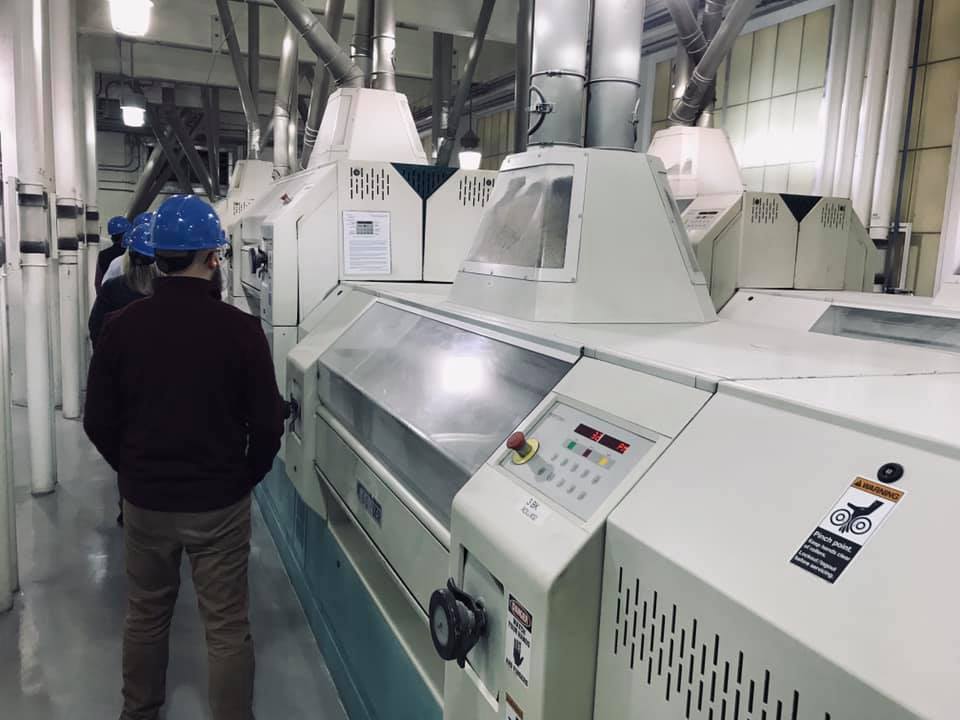
In the afternoon, we traveled north of Wichita to McPherson, Kansas, where we met at Cenex Harvest States (CHS) Refinery to learn about their two main goals: producing gasoline and diesel fuel. They produce about 100,000 barrels of product per day with a nearly 50/50 split between gas and diesel. There are 42 gallons per barrel; that is a daily production of 4.2 million gallons. Producing fuel is not an easy process. There are many chemical reactions that must take place for the production to be efficient and create the least amount of waste possible. They want to use as much of the crude as possible. Therefore, they produce many byproducts that are also put into containment and saved and sold as other fuels or used further in the refining process. We saw this complexity firsthand as we toured the refinery and observed the miles and miles of pipes and the multiple stops crude oil makes on its way to being high quality gasoline.
We then traveled south to Colwich, Kansas, and visited with ICM to learn about the ethanol industry. We first heard from Dave VanderGriend who started in the industry in 1978. ICM now produces one-third of the world’s ethanol and they have 21 patents granted for innovative technologies in the ethanol industry. They have an environmental mission. If ethanol was blended at 30% in gasoline, it would reduce emissions by almost 60%. They are also utilizing the entire corn kernel. They extract the oil, produce ethanol with the starch and use the protein to create better feeds for animals. ICM is a driver of the Urban Air Initiative where they are aggressively pushing for higher blends of ethanol by focusing on urban air pollution.
At ICM, we had the opportunity to hear from Josh Roe with Kansas Corn and Jesse McCurry with Kansas Grain Sorghum Producers. They briefly talked to us about their industry organizations and Jesse challenged the class with four questions: What concerns you the most about Oklahoma and Oklahoma agriculture? What have you learned about yourself and your classmates while in the OALP? How will you give back to the program? What are you willing to risk when your number is called to help solve challenges in agriculture?
We finished off day two with a wonderful dinner reception sponsored by Greg Reno, Teresa Randle and Jennie Bracken of American AgCredit.
Friday, Jan. 18, 2019
Day 3 of seminar 5 began with classmate Adam Cobb’s rendition of “Dancing Queen” by ABBA as his “punishment” for loading the bus late for the day’s activities. After his serenade, we made our way to American AgCredit.
We were introduced to Greg Reno, senior vice president of retail banking, who gave us a breakdown of the rest of his crew: Rich Gleason (20 years with AgCredit), Teresa Randal (with AgCredit since 2014), and Jennie Bracken (at AgCredit since her undergrad).
Greg explained that a passion for agriculture fuels all of them at American AgCredit. We watched a video on the impact of wildfires on farm families to get an idea of the kind of risk and needs that are causing farmers to seek loans. Greg gave an overview of the AgCredit system and history, including information about how farmers struggling during the depression were helped by the 1916 Farm Credit Act, which created 12 federal land banks and assisted with farm risk. This extends to today, where credit has flowed to 500,000 (ag-related) customers, representing ~40% of the debt in U.S. agriculture. This is a private/federal partnership arrangement with about $259 billion in total credit across the country.
Greg and his team explained different aspects of how loans work at AgCredit, how the different AgCredit agencies and territories are organized and change over time (through mergers and other alignments), and how the unique cooperative customer/member financing system operates. This appears similar to how Credit Unions pay members based on the amount of money they have invested at the institution, such that AgCredit borrowers can see 1% of their total loans as a distributed payment from AgCredit each year. Yet each member has only one vote, so the really large agricultural businesses do not always get to make decisions for the organization. We also learned about the diverse portfolio of members in AgCredit (wine, specialty crops, lumber, in addition to row crops and animals). Much of that diversity is due to territory across the western U.S., especially California and the new territory in Hawaii.
We did more Q&A with the team and watched a video about backwards bicycling to set up the final section of the event. AgCredit talked to us about our feedback on their strategy. As in the video, they wanted to see things from a fresh point of view. We had a lot more time for Q&A, which included some discussion of historic (1980s) and future-oriented topics.
Our final visit of the seminar was to the Wichita John Deere Training Center. Craig Hansen gave us an orientation. He also introduced his team, who spent the rest of the time with us. We had an overview of the U.S. and Canada training centers, history of the facility and introductions from the rest of the team of trainers.
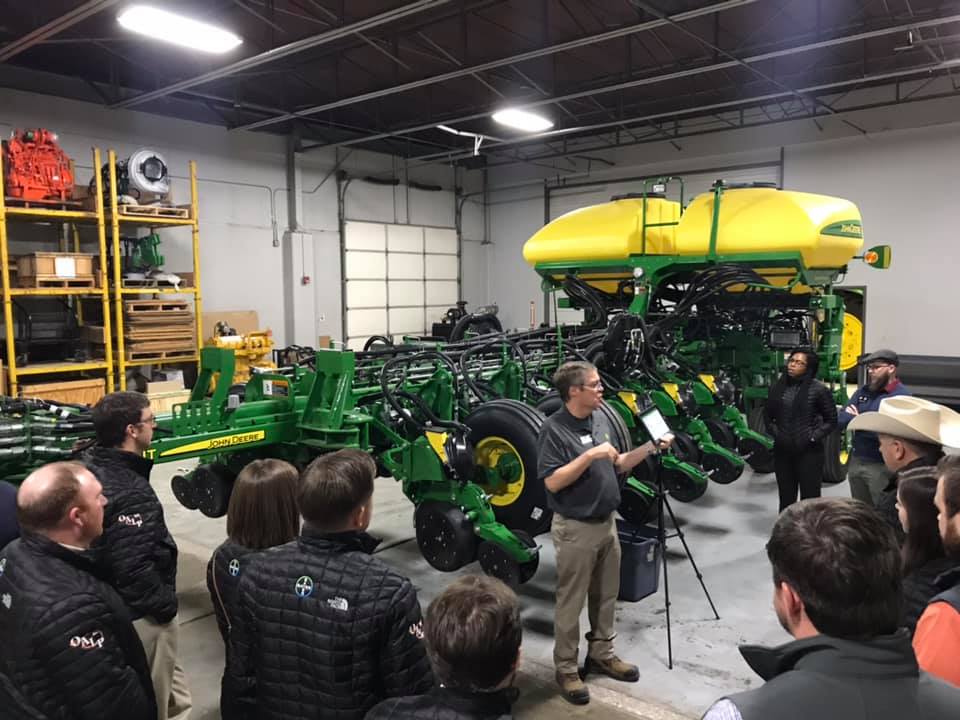
This gave us an idea of how people end up as J.D. trainers and how the training center delivers courses in person and at a distance. This was wrapped up pretty quickly after some Q&A, so we could take a tour of the facility. We had demonstrations of some of the technology, especially the sprayer and seeder functions of J.D. equipment. At least two of our classmates honked the loud horn of the giant tractor, which was jarring in an enclosed space! Finally, we took a picture outside on one of the tractors and then left for Stillwater.
In early March, class XIX will travel to Washington, D.C. for seminar six. We are looking forward to a week experiencing our nation’s capitol!
Kristin Young, Class XIX